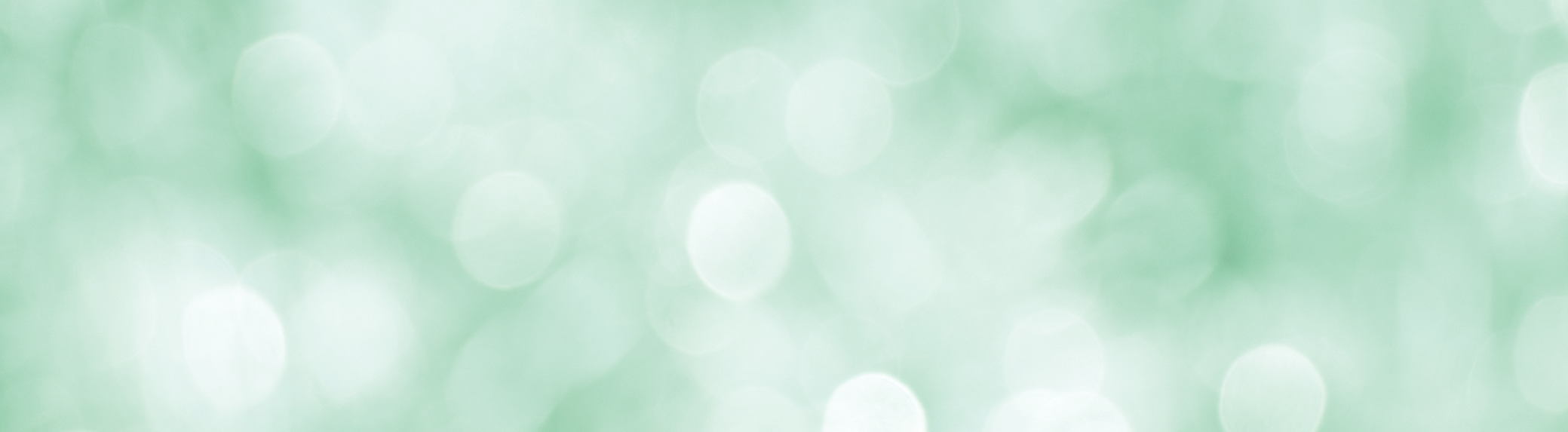
Processing
Organic production process to obtain purest quality products
Processing Systems
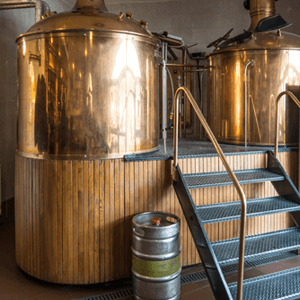
Technology plays a major role at every step, resulting in decreased production costs and increased yield. At Vanadurgi, innovation has resulted in numerous modifications to the diverse aspects of the Agarwood processing industry. The company has developed in-house technologies with the active assistance of its sister concerns. With the right use of technology, Vanadurgi produces superior quality products at reasonable prices, something that the industry looks forward to. The quality of essence depends on the quality of wood, the ago-climatic conditions where the trees are grown, and the extraction techniques adopted. Our tree-tech division works closely with wild tree suppliers and farmers to help them understand quality requirements so that the customers are assured of quality products.
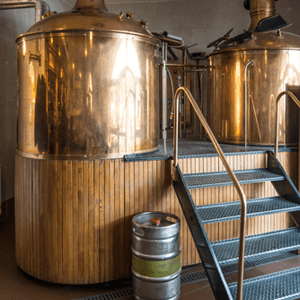
We accord utmost importance to proper pre-harvesting and post-harvesting techniques. The company follows a multilevel processing system comprising a cluster of independent primary processing units, an oil extraction factory, warehousing, and a packing and forwarding centre. Various grades of chips, flakes, powder, essential oils etc., are manufactured as per customer specifications at the primary processing units. The powder of uninfected wood and the leftovers of extraction will also be utilised for the manufacture of by-products.
The company has established a strong wild natural Agarwood sourcing network in the Assam, Nagaland, Mizoram, Tripura and Meghalaya states of Northeast India, where we have set up primary processing units in collaboration with our associates. In Karnataka, the plan is to set up primary processing centres in all the 24 taluks of the 7 districts where Agarwood is planted. In the first phase, processing arrangements have been made at one place in each district, which is at Alur, Kushalnagar, Thirthahalli, Sirsi, Chikmagalur, Sullia and Kundapur. Such units are established in collaboration with the company promoter of that particular region. The company is also planning to set up processing factories in the other south Indian states of Tamilnadu, Kerala, Goa, Maharashtra and Andhra Pradesh where small-scale cultivation is currently on.
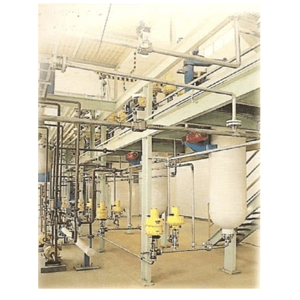
Chips Production
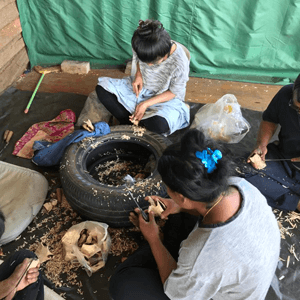
Quality is key element in the production of good quality resinous wood chips. We have kept priority to procure wild wood trees from Assam, Megalaya, Tripura and Nagaland province of north east India. Such Agarwood logs from suppliers are segregated at our associated facility into chips and extraction grade depending on resin content in the material. We focus on each and every step as right from harvesting after the completion of winter, when the trees have the maximum oil content. All these collective efforts leading to the production of best quality wild wood Chips.
The company is establishing a cluster of primary processing centres in the dense plantation zones of Karnataka for the production of cultivated Agar wood chips. As soon as the infected trunks of inoculated trees are harvested, small twigs are separated from them, and the stem is cut into pieces 1 to 2 metres long, weighing around 10 to 20 kg each. They are then transported to the nearest primary processing station which has skilled labour and supporting facilities. Trees are slit and infected, and the non-infected parts are separated using indigenous tools. Arrangements are made to process the trees into different grades in the presence of growers. The infected wood is then graded according to industry standards as soft yellowish white material, average quality brown ones, and blackish parts which can be used for making chips.
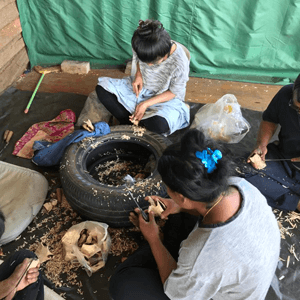
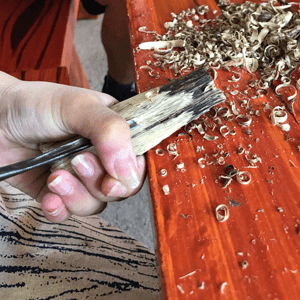
At a prime plantation zone of Karnataka province company has set up primary processing units. A standard Chips production and resinous wood extraction facility that will roll out several tons of the daily production is coming up. Resinous wood Chips from all the primary processing units are polished and sent for modern processing at Bangalore, and are finally packed and forwarded to customer destinations. And lower grades which are not edible for chips are extracted for oil through the modern process to get super grades of oil. Quality of our cultivated wood is almost similar quality that of medium quality wild wood and available for reasonable price as well.
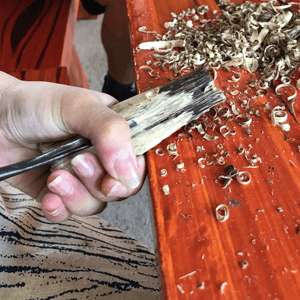
Oil Distillation
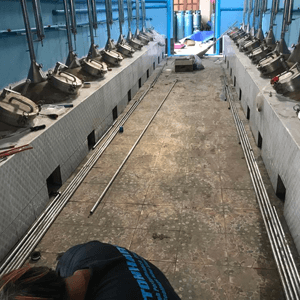
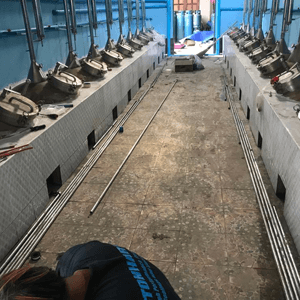
As a first step, wood is segregated into various grades depending on resin density, and each grade is separately used for extraction. The wood is chopped and dehumidified with electrical dryers, or in semi-shaded sunlight, for 3 to 4 days, and 3 to 4 hours per day. Later, the chopped bits are crushed into about 1 mm grains to increase the surface area of extraction. Based on odour requirements, the material is soaked in a pot for 200 to 400 hours for fermentation. Depending on the distilling capacity and the quality of wood, the material is loaded into extraction vessels to get the best recovery.
Agar Boya or Agar wax is extracted from the non-infected white wood. We have set up 500 to 1,000 kg capacity units at some of our primary processing factories. After chopping the trunk and grading the wood, leftover white sap wood is cut into smaller pieces of 2 to 3 cm length, and about 0.5 thickness. The material is then soaked in the fermentation vessel for 2 to 3 weeks, and extracted through the hydro distillation vessel which works on firewood.
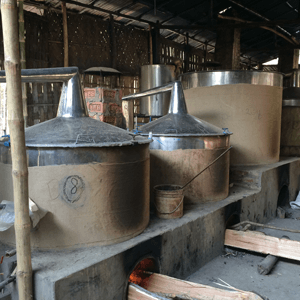
Value Addition
The company is following the cryogenic powdering system in the facility in Bangalore for the powdering of superior grades of resinous wood. The temperature of the Agarwood powder in the general grinding process which does not use a cooling system can reach up to +70 degrees. Such a high temperature will reduce volatile components and heat-sensitive constituents in the Agarwood powder. This process does not damage or alter the chemical composition of the main elements in any way. The process involves cooling or chilling a material by dry ice or liquid nitrogen, and then reducing it to the size of a small particle. In the first stage, the cryogenic grinding machine powders the elements at sub-zero temperatures ranging from 0-10°C. The elements are then frozen with liquid nitrogen, as they are finally being ground to particles without disturbing the volatile and heat-sensitive constituents of the wood.
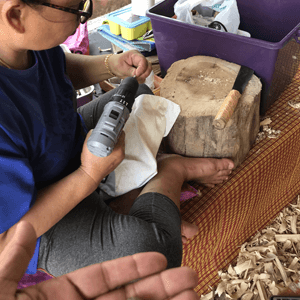
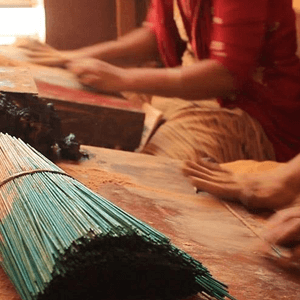
In order to get the best quality product and highest recovery, superior grades of chips are extracted in the Super Critical Fluid Extraction (SCFE) system using carbon-di-oxide as a solvent. SCFE is the process of separating one compound, that is oil, from another compound, that is Agarwood powder, using supercritical fluids as the extracting solvents. The supercritical fluid state occurs when a fluid is above its critical temperature and critical pressure when it is between the typical gas and liquid state. Manipulating the temperature and pressure of the fluid can solubilise the Agarwood mix and selectively extract it. Agarwood powder is loaded in the extraction vessel and pressurised with CO2 to dissolve. It is then transferred to a fraction collector, where the contents are depressurised, and the CO2 loses its solvating power, causing the desired material to precipitate. The condensed CO2 can be recycled for use with the next batch.
Sister concern companies of Vandurgi are engaged in the production of value added products. The main products we manufacture are Incense sticks, Agarwood Cones, Gaharu coils, beads, are some of the products we manufacture at our facilities. Products range also includes Deh-al-Oudh, Perfume which is manufactured together with our associated perfumers. At Chikmagalur, the company is setting up a new facility for the manufacturing of value-added Agarwood products, packing and forwarding set ups. Consumer products are manufactured as per requirements of our distribution channels. And similar products can also be offered to our channel parters as per their brand requirements.
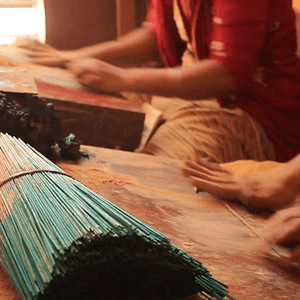